Warehousing plays a pivotal role in the logistics and supply chain sectors.
Each type of warehouse has unique characteristics, catering to different needs in the transportation and storage of goods.
Here at Compare the Carrier we understand this as it’s one of the most crucial factors for the efficient drayage and freight process. Exploring the vast landscape of warehousing solutions is pivotal in optimizing supply chain management and enhancing logistics efficiency. This guide delves into warehousing types, including smart warehouses, that are fundamental in supporting e-commerce warehousing and streamlining operations. Also their functions, and their relevance in the logistics industry.
So buckle up!
Types of Warehouses
Warehouses are categorized based on their specific functions, who owns them, and the unique services they offer. This categorization covers a wide range of facilities, from government-operated warehouses to technologically advanced smart warehouses, each serving a unique purpose in the broader context of supply chain management. So let’s dive in:
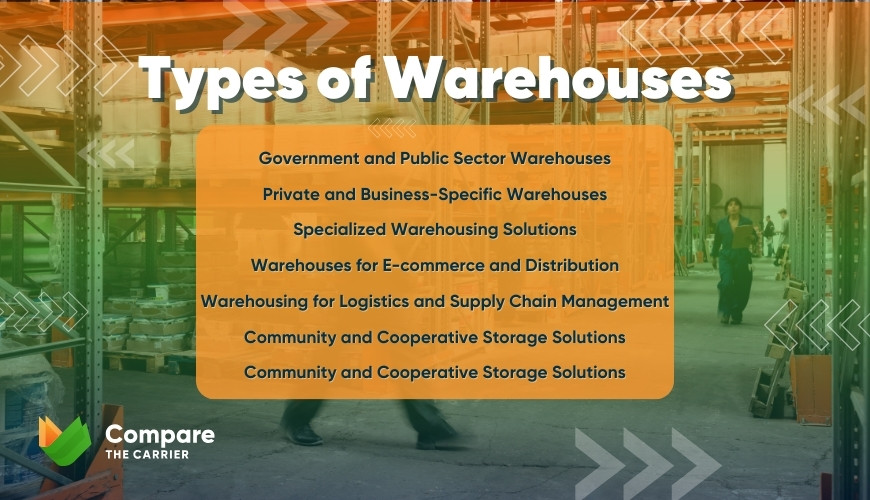
Government and Public Sector Warehouses:
Government Warehouses
Overview: Government warehouses are large-scale facilities used by federal or local governments.
Functions: They primarily store government supplies, emergency kits, and materials for public service operations.
Capacity: In the US, these types of warehouses occupy a significant portion of the total warehouse space, reflecting their importance in national logistics.
Utilization: Often used for disaster relief, storing road maintenance supplies, and housing administrative goods.
Public Warehouses
Definition: Also known as 3PL (Third-Party Logistics) warehouses, these are operated by independent entities and rented out to various businesses.
Flexibility and Cost: This type of warehouses offer flexible storage solutions with lower upfront costs, ideal for SMEs and businesses with variable storage demands.
Services Offered: Often provide additional logistics services like transportation and handling, beneficial for companies without dedicated logistics departments.
Limitations: Less control over storage and handling processes compared to private warehouses.
Private and Business-Specific Warehouses:
Private Warehouses
Ownership and Operation: Owned by the companies that produce the goods stored within them, offering full control over operations.
Benefits: Provide heightened security and customization for storage and handling of products.
Investment and ROI: While they require substantial initial investment, they can be more cost-effective in the long term for large businesses with consistent storage needs.
Challenges: High setup and maintenance costs; not flexible for businesses with fluctuating storage needs.
Contract Warehouses
Nature: These types of warehouses are service-oriented, offering dedicated space and services based on contractual agreements.
Guaranteed Space: Provide assured storage space, critical during peak seasons or unexpected demand surges.
Services: Often include value-added services like kitting, packaging, and inventory management.
Cost Implication: More cost-effective than public warehouses for long-term needs, but generally pricier than managing a private warehouse.
Specialized Warehousing Solutions:
Bonded Warehouses
Purpose: Specialized warehouses for storing imported goods before duties or taxes are paid.
Regulations: Heavily regulated to ensure compliance with customs laws.
Ideal For: Businesses involved in international trade, allowing them to defer duty payment until goods are sold.
Types: Includes storage for general merchandise, bulk commodities, and specialized items like grain or perishable goods.
Hazmat Warehouses
Specialization: Designed to store hazardous materials, such as chemicals, gasses, explosives, radioactive and biological substances.
Safety Measures: These warehouses are equipped with specialized climate control, extra spacing between items, robust security, and staff trained in handling hazardous materials.
Location: Often situated away from densely populated areas to mitigate risk.
Cost Implications: Operating and storing materials in hazmat warehouses can be expensive, limiting their use primarily to large corporations or government entities.
Climate-Controlled Warehouses
Specialization: Designed to store goods requiring specific temperature or humidity conditions.
Products Stored: Includes food items, pharmaceuticals, and sensitive electronics.
Infrastructure: Equipped with advanced HVAC systems, insulation, and monitoring technology.
Cost Factor: More expensive to operate due to specialized equipment and energy usage.
Smart Warehouses
Technology Integration: Utilize advanced technologies like Automated Storage and Retrieval Systems (ASRS), Autonomous Mobile Robots (AMRs), and sophisticated Warehouse Management Systems (WMS).
Efficiency: Highly efficient with reduced labor requirements, these warehouses minimize human error and enhance overall productivity.
Investment: The initial cost of automation can be high, and there is a dependency on technology, which can pose risks in case of malfunctions.
Warehouses for E-commerce and Distribution:
Fulfillment Centers
Designed For: Specifically tailored for e-commerce businesses, managing the entire order fulfillment process.
Services: Includes receiving, storing, processing, and shipping orders directly to consumers.
Efficiency: Streamline the supply chain by reducing the time between an order being placed and shipped.
Example: Amazon’s fulfillment centers are a prime example, offering storage and direct shipping for third-party sellers.
Distribution Centers
Function: Act as a hub for storing and distributing products to retailers or directly to consumers.
Speed: Designed for rapid turnover of goods, focusing on efficient order processing and delivery.
Technology: Often equipped with advanced logistics technology for tracking and managing inventory.
Suitability: Best for businesses with high-volume distribution needs, like large retail chains or e-commerce giants.
Warehousing for Logistics and Supply Chain Management:
Cross-Docking Warehouses
Process: Involve minimal storage, with goods transferred directly from inbound to outbound transportation.
Efficiency: Reduce handling costs and storage time, optimizing the supply chain.
Application: Ideal for perishable goods or high-demand products requiring rapid delivery.
Limitation: Requires precise coordination and timing, making it complex to manage.
Reverse Logistics Warehouses
Purpose: These facilities specialize in managing the return process of goods. They handle the sorting, repackaging, recycling, refurbishing, or destruction of returned items.
Benefits: Improves customer satisfaction by offering a smooth return process and helps in recovering value from returned products.
Challenges: Managing reverse logistics can be complex due to the need for efficient sorting and processing systems.
Community and Cooperative Storage Solutions:
Owned and Operated By: Typically run by cooperative groups like farmers or local producers.
Cost-Effectiveness: Offer reduced storage rates for members, pooling resources for better affordability.
Community Focus: Often cater to local or regional distribution needs, supporting smaller businesses and producers.
Access: May be limited compared to more commercial warehousing options.
Choosing the Right Warehouse
When selecting the right warehouse type for your business, it’s important to consider several key factors to ensure that the chosen facility aligns with your specific needs and objectives.
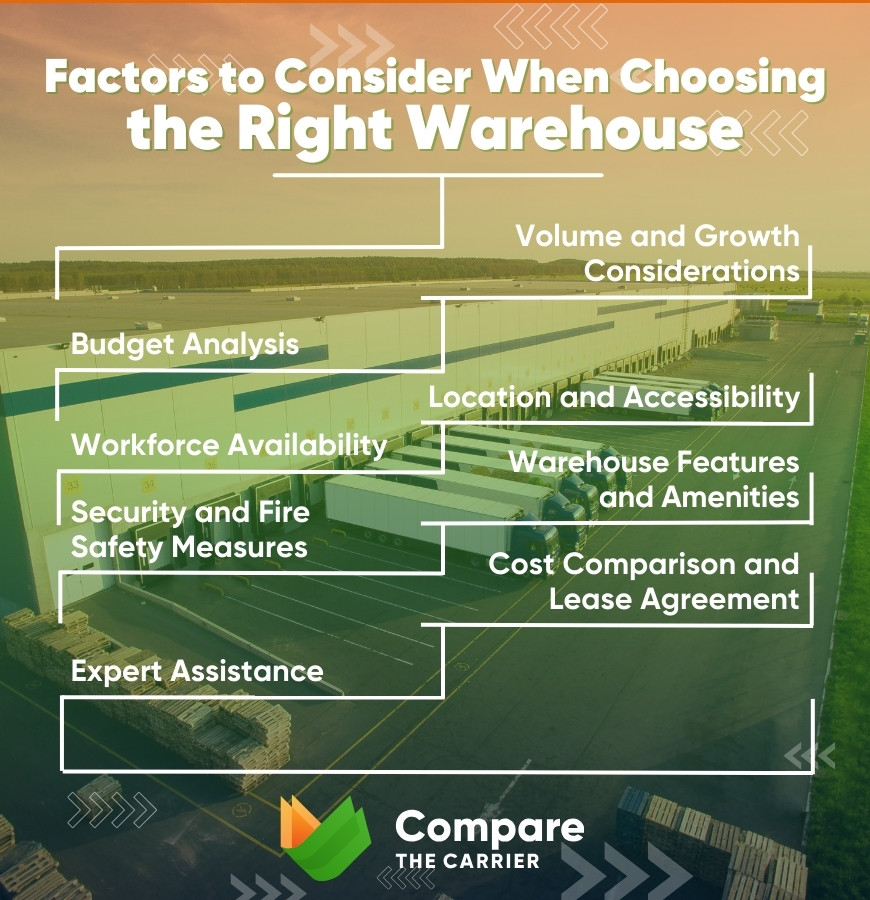
Volume and Growth Considerations
Assess the size of your inventory and the frequency of your shipments. It’s crucial to choose a warehouse type that can not only accommodate your current inventory but also has the flexibility to adapt to your business’s growth. This might include scalable space and the ability to handle increased throughput without disrupting operations.
Budget Analysis
Before choosing a warehouse type, consider all associated costs, including rent, utilities, equipment, and labor. It’s essential to have a clear understanding of your financial limitations and the total operating expenses involved in running the warehouse.
Location and Accessibility
The warehouse’s location should be strategically chosen based on proximity to suppliers, customers, and major transportation routes like highways, rail yards, or airports. This not only improves supply chain efficiency but also enhances customer satisfaction due to faster order fulfillment.
Workforce Availability
Evaluate the local labor market to ensure there’s a skilled workforce available. This aspect is critical for efficient warehouse operations and should be considered alongside other factors like public transportation routes for employee accessibility.
Warehouse Features and Amenities
Pay attention to the warehouse’s layout, organization, and available technology. Advanced warehouse management systems can greatly enhance operational efficiency by optimizing inventory levels and automating various tasks. Additionally, assess the available equipment, such as forklifts and conveyor belts, necessary for your specific operations.
Security and Fire Safety Measures
Ensure robust security measures are in place, including physical barriers, surveillance systems, and fire safety protocols. These measures are crucial for protecting your inventory from theft, damage, and other risks.
Cost Comparison and Lease Agreement
When finalizing your decision, compare the costs of potential warehouses and review their lease terms carefully. Make sure you understand all aspects of the agreement and how they align with your business objectives.
Expert Assistance
Given the complexities involved in setting up or moving to a new warehouse, seeking help from logistics experts or solution providers can be immensely beneficial. They can assist with logistics, inventory management, staffing needs, and more.
Choosing the right warehouse type involves a thorough evaluation of your business needs, careful budget planning, consideration of location and accessibility, assessment of available features and security measures, and possibly seeking expert advice. By carefully analyzing these factors, you can select a warehouse that effectively supports your business operations and growth strategies.
Conclusion
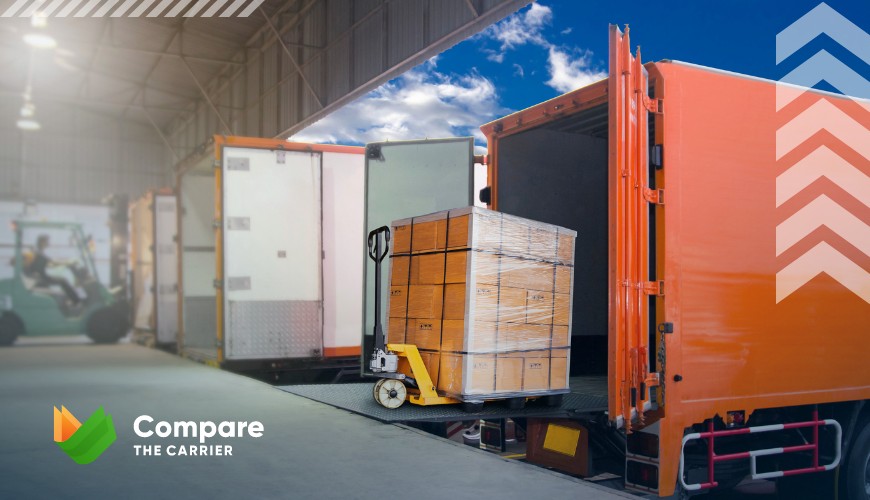
Understanding the diverse types of warehouses is crucial in the world of logistics and supply chain management. Each type of warehouse serves specific needs, from government storage facilities to technologically advanced smart warehouses. Companies like Compare The Carrier can leverage this knowledge to optimize their logistics services, ensuring efficient freight and drayage operations. As the industry evolves, staying informed about different warehouse types and their functionalities becomes vital for businesses to remain competitive and responsive to market demands.
Integrating Compare The Carrier into your container drayage and freight process adds significant value. Compare The Carrier specializes in simplifying the logistics process by offering expert guidance in selecting the most appropriate warehouse solutions and drayage services. Our platform connects you with a network of professional carriers and warehouses, ensuring that your logistics needs are met with efficiency and reliability.
With Compare The Carrier, businesses can benefit from a streamlined approach to logistics, including real-time tracking, effective communication, and customized solutions. This not only optimizes the logistics process but also enhances overall business operations, making it an indispensable tool for companies seeking to improve their supply chain efficiency and cost-effectiveness.
FAQ
How does Compare The Carrier choose its warehousing partners for logistics solutions?
Compare The Carrier selects warehousing partners based on their efficiency, technological advancements, and their ability to provide scalable solutions for e-commerce and other sectors.
Can Compare The Carrier help with logistics efficiency for small businesses?
Yes, Compare The Carrier offers tailored logistics and warehousing solutions to improve efficiency for businesses of all sizes, leveraging technology and strategic partnerships to optimize supply chain management.
What are smart warehouses and how do they differ from traditional warehouses?
Smart warehouses utilize automation and digital technology, such as IoT devices, robotics, and AI, to increase efficiency and reduce human error, contrasting traditional warehouses that rely more on manual processes.
Can e-commerce businesses benefit from specific warehousing strategies?
Yes, e-commerce warehousing strategies focus on managing a wide variety of stock keeping units (SKUs), handling returns efficiently, and optimizing for quick dispatch to meet the fast-paced demand of online shoppers.
What is logistics efficiency and how can it be improved through warehousing?
Logistics efficiency refers to optimizing operations to reduce costs and speed up delivery times. It can be improved through warehousing by implementing automated systems, optimizing layout and inventory management, and integrating advanced tracking technologies.
What technologies are commonly used in smart warehouses?
Technologies such as automated guided vehicles (AGVs), drones, warehouse management systems (WMS), robotics, and artificial intelligence (AI) are commonly used in smart warehouses to improve efficiency and accuracy.