In 2024, U.S. warehouse and distribution center downtime due to inefficient loading dock operations was estimated to cost the logistics industry over $3.5 billion annually, according to data from Logistics Management and the Council of Supply Chain Management Professionals. These losses stem from delays in shipments, equipment failures, employee injuries, and energy inefficiencies. For facilities operating on tight margins and even tighter timelines, this is more than an inconvenience—it’s a competitive disadvantage.
The loading dock is the heartbeat of any warehouse or fulfillment center. Whether you’re processing dozens or thousands of shipments daily, the effectiveness of your loading dock determines everything from turnaround time to cargo safety. An underperforming dock invites costly bottlenecks, damaged goods, and workplace hazards.
To help commercial and industrial facility operators avoid those pitfalls, we’ve outlined ten must-have elements every efficient loading dock should prioritize. From critical hardware like dock leveler springs to freight carrier coordination — and even smart software like the auto lead tool by CompareTheCarrier — each component plays a role in ensuring your dock operations are fast, safe, and future-ready.
1. High-Quality Dock Levelers
Why Dock Levelers Matter
A dock leveler acts as the bridge between your warehouse floor and the trailer bed of a truck. It compensates for height differences between the dock and the vehicle, ensuring smooth, safe loading and unloading. When functioning properly, it provides continuity between the building and the transport vehicle—boosting workflow efficiency, minimizing material handling delays, and reducing the likelihood of employee injuries.
A quality dock leveler also absorbs the shock and vibration that occurs when forklifts and pallet jacks cross the threshold. This not only improves operator comfort but extends the lifespan of your material handling equipment. Conversely, a faulty or outdated dock leveler compromises both safety and productivity.
Consider this: a Wisconsin-based distribution center reported a 42% reduction in operational downtime after proactively replacing aging dock levelers with more robust, low-maintenance models. This move not only increased safety scores but also improved truck turnaround times by over 20%. For facilities comparing carrier costs alongside hardware investments, accurate vehicle transportation rates can also play a key role in budgeting and logistics planning.
Common Dock Leveler Issues
Despite their heavy-duty design, dock levelers are subject to wear and tear—especially in high-volume facilities. Key components like hold-down devices, lip extensions, and hinges often bear the brunt of repetitive motion and load strain. Among the most common issues:
- Worn Dock Leveler Springs – Springs that support the platform can weaken, causing uneven elevation and dangerous collapses.
- Leaking Hydraulic Cylinders – Hydraulic fluid leaks not only reduce lift capacity but pose environmental and safety hazards.
- Misaligned or Broken Retention Systems – These systems hold the leveler in place when not in use. A malfunction here can lead to dock leveler free fall, damaging goods and injuring personnel.
- Rust or Corrosion on Frame and Lip – Especially in open or semi-exposed docks, moisture can corrode steel structures, compromising the leveler’s integrity.
Routine inspections can catch these issues early—but once major components begin to fail, full replacement is often the most cost-effective option. Investing in high-quality dock levelers that meet or exceed OEM standards helps prevent repeated repairs and unplanned outages.
Tip: Ensure your dock leveler is compatible with your typical trailer height and weight loads. Overloading or under-sizing equipment is a leading cause of accelerated wear.
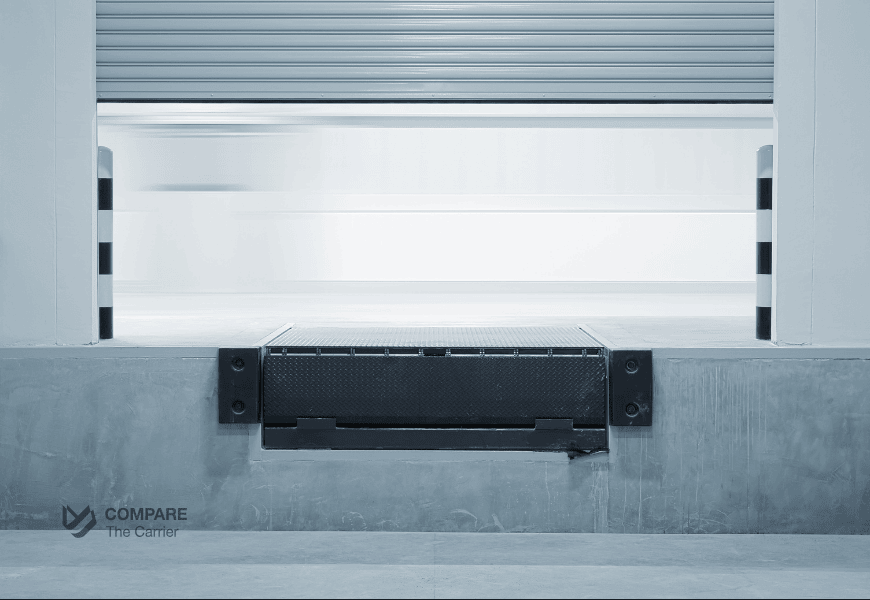
2. Reliable Dock Leveler Springs
The Role of Dock Leveler Springs
Dock leveler springs may be small in size, but they play a massive role in keeping your operations stable, safe, and efficient. These springs are responsible for counterbalancing the weight of the dock leveler platform, allowing it to raise and lower smoothly with minimal manual or mechanical force.
In mechanical dock levelers, dock leveler springs are the primary force that lifts and supports the platform. They bear the daily brunt of forklift traffic, cargo loads, and constant movement. Without well-functioning springs, even the highest-quality dock leveler becomes a hazard waiting to happen.
A fatigued or broken spring can cause the platform to become misaligned, sticky, or unsafe to use—putting personnel and shipments at risk. And since these springs are under extreme tension, a failure can occur suddenly and dangerously if not maintained.
When to Replace & Why It Matters
Like tires on a truck, dock leveler springs don’t last forever. Facility managers should be proactive in inspecting and replacing springs before they snap or lose their tension.
Signs a Spring Needs Replacement:
- The dock leveler platform drops suddenly or unevenly
- Springs appear stretched, corroded, or cracked
- The platform doesn’t stay in a raised position
- Noticeable jerking motion during operation
- Loud creaking or snapping sounds
Ignoring these signs can result in:
- Injuries from platform instability or failure
- Equipment damage as forklifts collide with misaligned decks
- Costly repairs to the leveler structure or hydraulics
- Unexpected downtime that disrupts shipping schedules
According to FMCSA safety recommendations, all mechanical dock levelers should be inspected monthly, with springs evaluated for fatigue, tension, and visible wear.
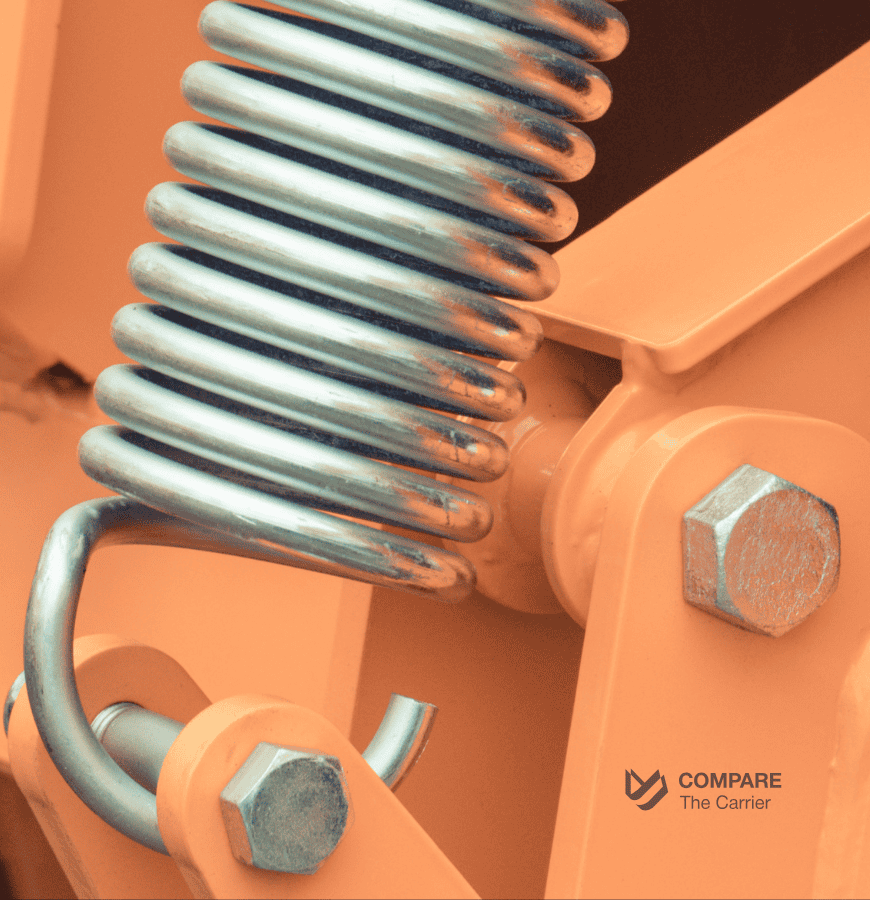
The Case for Stocking Spare Dock Leveler Springs
Considering how vital they are, having spare dock leveler springs on hand can mean the difference between a 15-minute repair and a 2-day shutdown waiting on delivery. A warehouse in Ohio saved over $4,500 in one quarter simply by keeping a backup spring kit on-site, reducing both labor costs and freight delays during peak season.
Many OEM and aftermarket suppliers offer spring kits tailored to specific dock models—ensuring compatibility and safe performance. For the best results, choose parts that meet or exceed the original manufacturer’s specifications.
Remember: Always de-tension springs before attempting replacement. Dock springs are under extreme pressure and should be handled only by trained personnel.
3. Durable Dock Seals and Shelters
Protection Against External Elements
Dock seals and shelters may not be the most glamorous equipment on your loading dock, but they serve as the first line of defense against environmental threats that can seriously impact your operation. These protective accessories create a tight seal between the trailer and your facility’s dock door, shielding interior spaces from rain, snow, wind, dust, and pests.
Whether your facility operates in humid Louisiana or snowy Minnesota, durable dock seals and shelters help preserve product quality and maintain indoor air conditions—both essential in food-grade, pharmaceutical, or climate-sensitive storage environments.
According to a Department of Energy report, buildings lose up to 30% of their heating and cooling energy through poorly sealed openings. For warehouses with high dock traffic, this energy loss is amplified—and so are the utility costs.
A well-fitted dock shelter accommodates a wider range of trailer heights and widths, while seals offer a snug fit for standard-size trailers. Choosing the right system depends on your typical freight profile and loading frequency.
Operational & Energy Efficiency
Beyond climate control, dock seals and shelters provide additional operational benefits:
- Reduced Slips and Falls: By keeping moisture and debris out, floor surfaces stay dry and safe for foot and forklift traffic.
- Increased Visibility: When combined with dock lighting, enclosed shelters can eliminate harsh glare or backlighting issues.
- Lower Maintenance Costs: Cleaner dock areas reduce the strain on HVAC systems and prevent rust or corrosion on dock parts.
Example: A cold storage facility in Illinois decreased its annual energy spend by over 18% after upgrading to insulated dock shelters with foam compression seals. The facility also reported fewer weather-related inventory incidents during harsh winter months.
When selecting dock seals and shelters:
- Choose materials rated for your region’s weather and temperature ranges
- Make sure foam compression or inflatable seals are correctly matched to trailer types
- Inspect quarterly for tears, gaps, or compression loss
Tip: Seals and shelters not only protect goods but also extend the life of loading dock parts by keeping corrosive elements at bay—especially in open or semi-exposed docks.
4. Proper Dock Lighting
Safety & Visibility First
Proper dock lighting is essential—not optional—when it comes to safe and efficient operations. Warehouses operate around the clock, and many dock areas are located in enclosed or poorly lit spaces. Without adequate lighting, the risk of injuries, forklift accidents, and shipping errors increases dramatically.
The Occupational Safety and Health Administration (OSHA) requires that general warehouse lighting be sufficient to clearly illuminate working surfaces. Poor lighting in loading docks can result in:
- Misalignment between trailers and dock levelers
- Missed hazards such as loose debris or fluid spills
- Improper loading and unloading that damages goods
- Forklift operator blind spots or navigation errors
In fact, according to the National Safety Council, visibility-related incidents account for over 20% of dock-related injuries in the U.S. each year. Investing in proper lighting is a direct investment in worker safety and facility uptime.
LED Upgrades & ROI
The shift to LED dock lights has become a best practice across modern facilities—and for good reason. LEDs offer numerous advantages over traditional incandescent or halogen lighting systems:
- Energy Efficiency: LEDs use up to 75% less energy than traditional lighting, helping to reduce utility bills substantially.
- Longevity: A quality LED fixture can last over 50,000 hours, reducing maintenance downtime and replacement costs.
- Instant-On: Unlike older systems, LEDs light up immediately with no warm-up time, keeping workflows uninterrupted.
- Brightness and Directionality: Adjustable LED dock arms allow you to direct light exactly where it’s needed—into trailers, across platforms, or along footpaths.
Case Study: A logistics hub in Georgia reported a 38% drop in lighting-related maintenance calls after switching to LED dock arms with motion sensors. The change also reduced the facility’s lighting energy consumption by 28% annually, recouping the investment in under 18 months.
For best results, consider layering your lighting plan:
- Task Lighting: LED dock arms that extend into the trailer for direct visibility
- Area Lighting: Overhead LEDs for ambient dock area coverage
- Emergency Lighting: Backup systems in case of power loss
Tip: Always check lighting compatibility with any dock accessories or barriers in place. Shadows or blocked beams can defeat even the best fixtures.
5. Dock Locks and Vehicle Restraint Systems
Compliance with FMCSA and OSHA
When a trailer isn’t properly secured at the dock, it’s not just a logistics issue—it’s a serious safety risk. Dock locks and vehicle restraint systems are essential for complying with FMCSA (Federal Motor Carrier Safety Administration) and OSHA standards, which mandate that trailers be properly secured during loading and unloading to prevent unexpected movement.
According to OSHA regulation 29 CFR 1910.178(m)(7), trailers must be immobilized or restrained before being entered by a forklift. Violating this can lead to significant fines and—more importantly—worker injuries or fatalities.
Vehicle restraints lock onto a trailer’s rear impact guard (also known as the ICC bar) or tires, anchoring it to the loading dock. When paired with automatic signals and interlocks, they ensure that forklifts only enter trailers that are fully secured.
Injury and Accident Prevention
Trailer creep, premature departure, and landing gear collapse are all risks that can be eliminated with a proper vehicle restraint system. Here’s how:
- Trailer Creep: Constant movement from forklift entry/exit causes the trailer to gradually inch away from the dock.
- Early Departure: If a truck driver pulls away before the loading is complete, it can cause a forklift to fall off the dock—a leading cause of fatal warehouse accidents.
- Trailer Pop-Up: Uneven weight distribution from forklifts can cause unrestrained trailers to tilt or shift dangerously.
According to the National Institute for Occupational Safety and Health (NIOSH), using a dock lock can reduce the risk of forklift-related dock accidents by up to 90%.
Types of Vehicle Restraint Systems:
- Manual Wheel Chocks: Low-cost but less secure and highly dependent on user compliance.
- Mechanical Restraints: Engage manually but lock automatically with trailer ICC bars.
- Hydraulic or Electric Restraints: Fully automated and integrated with dock control panels and signaling lights.
A Tennessee-based beverage distributor saw a 62% drop in near-miss reports after installing hydraulic dock locks with integrated red/green LED indicators—clearly signaling when a trailer is safely locked or not.
Tip: For added safety, connect vehicle restraints with your dock leveler controls, so the leveler can only be operated when the trailer is securely locked in place.
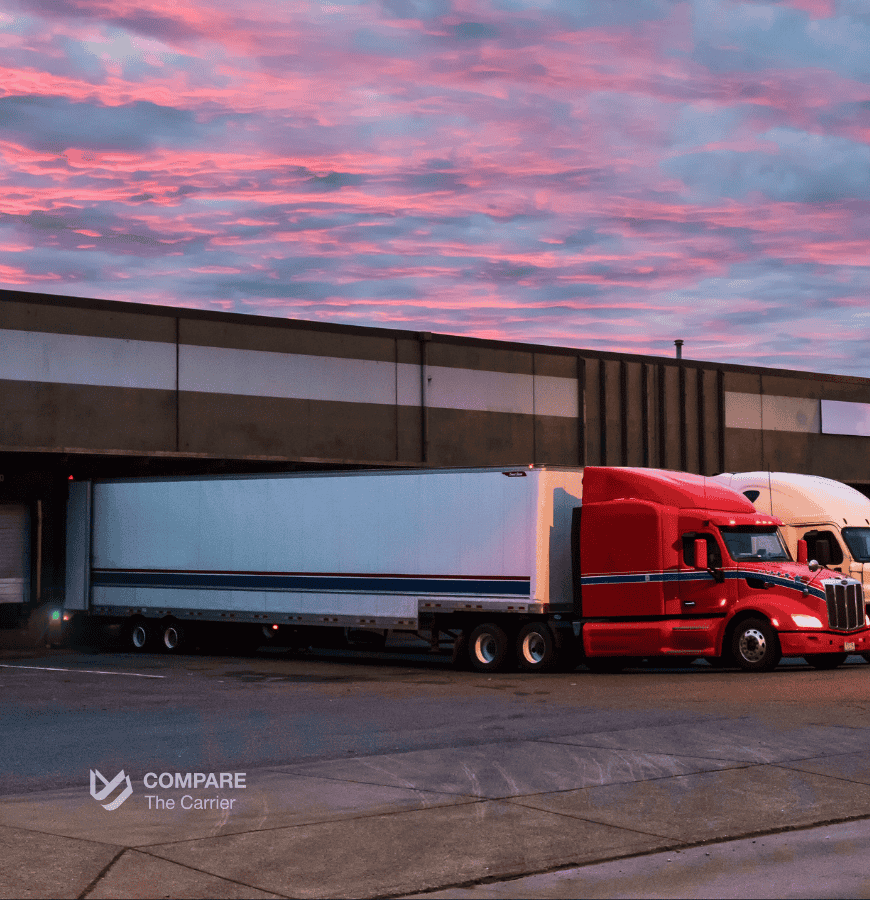
6. Maintenance and Inspection Routines
Scheduled Dock Audits
No matter how advanced your dock equipment is, it’s only as effective as the maintenance that supports it. Establishing consistent maintenance and inspection routines is key to keeping operations running smoothly—and safely.
A loading dock audit typically involves checking all mechanical, electrical, and structural systems for wear, misalignment, corrosion, or malfunction. These audits should be performed monthly for high-traffic docks and at least quarterly for standard-use facilities, following OSHA guidelines and manufacturer recommendations.
Regular inspections help catch issues early, reducing the likelihood of unexpected equipment failure that can cause:
- Shipping delays
- Product damage
- Worker injuries
- Emergency repair costs
Example: A Midwestern manufacturing plant saved an estimated $27,000 annually by instituting a preventative maintenance program that identified early wear in dock leveler springs and seals before full failures occurred.
Sample Maintenance Checklist
Here’s a sample checklist to include in your dock maintenance plan:
Dock Equipment:
- Check dock leveler springs for fatigue or breakage
- Inspect hold-down mechanisms and hydraulic fluid levels
- Test lip extension and retraction movement
- Look for weld cracks or corrosion on levelers
Restraints & Safety Systems:
- Confirm proper function of dock locks and vehicle restraints
- Test red/green LED indicator lights
- Check wheel chocks (if used) for visibility and stability
Electrical & Lighting:
- Replace dim or flickering dock lights (preferably with LED)
- Check emergency backup lighting functionality
- Inspect wiring for signs of wear or exposure
Structural Components:
- Examine dock seals and shelters for rips or sagging
- Check bumpers for compression or damage
- Inspect dock plate or leveler pit for debris buildup or rust
Administrative:
- Log inspection findings and schedule follow-ups
- Maintain maintenance records for safety audits and insurance
Tip: Assign one or more trained personnel to lead maintenance inspections. Many facilities pair this with a digital CMMS (Computerized Maintenance Management System) to automate reminders and record-keeping.
Routine dock upkeep not only extends the lifespan of your loading dock parts, it prevents unplanned downtime—a cost far greater than regular maintenance ever will be.
7. Spare Loading Dock Parts On Hand
Why Preparation Saves Money
One of the fastest ways to derail productivity is waiting on replacement parts for failed dock equipment. Unplanned downtime—especially during peak shipping periods—can cost thousands of dollars per hour in lost throughput, idle labor, and late delivery penalties.
Keeping spare loading dock parts in inventory is a simple, high-ROI strategy that ensures quick repairs and uninterrupted operations. While some facilities may hesitate to tie up budget in inventory, the cost of downtime almost always exceeds the cost of preparation.
Real-World Example: A distribution center in Texas reported savings of over $18,000 in avoided downtime in a single year after implementing a “critical parts bin” for frequently failing items like dock leveler springs and dock lights.
According to industry estimates, having a stocked inventory of key loading dock parts reduces repair wait times by up to 70%.
What to Keep in Stock
Every dock is different, but there are common components that should be readily available across most warehouse types. Here’s a basic list of what your facility should consider keeping on-site:
Essential Spare Dock Equipment Parts:
- Dock leveler springs (matched to specific models)
- Hold-down assemblies and ratchets
- Hydraulic pump kits and fluid
- Lip assist rods and lip pins
- Dock bumpers and mounting hardware
- Dock locks and ICC bar parts
Electrical and Lighting Components:
- LED dock lights and mounting arms
- Light indicator lenses (red/green)
- Power cords, fuses, and basic wiring
Sealing and Safety Accessories:
- Dock shelter gaskets
- Door seals and foam compression units
- Vehicle restraint control modules
Keyword note: Sourcing reliable parts for loading docks that meet OEM specifications ensures compatibility and durability. Subpar or ill-fitting components can lead to repeat failures or costly safety violations.
How to Store & Organize
- Label clearly by dock number or equipment type
- Store in climate-controlled areas to avoid rust or moisture damage
- Rotate inventory to prevent part degradation
- Digitize your stock using inventory software or spreadsheets
Facilities with smart stocking systems dramatically reduce downtime by empowering their maintenance teams to act fast—and avoid the scramble for expedited shipping fees or after-hours service calls.
8. Training Dock Personnel
Human Error Risks
Even the most advanced loading dock system can’t compensate for improper human operation. In fact, according to the Bureau of Labor Statistics, nearly 25% of dock-related injuries stem from user error—often due to inadequate training or unfamiliarity with equipment.
Untrained or undertrained personnel are more likely to:
- Misuse dock levelers or vehicle restraints
- Operate forklifts recklessly around open docks
- Skip safety protocols like securing trailers or using wheel chocks
- Overlook warning signs of failing loading dock parts
These errors don’t just slow down workflow—they introduce major safety and liability concerns. In worst-case scenarios, a simple mistake can lead to falls from height, crushed limbs, or overturned forklifts, which are among the top OSHA-cited incidents at warehouses.
Ongoing Training Benefits
Creating a formal and continuous dock training program doesn’t have to be complicated or costly—but it does need to be consistent. Investing in your team’s knowledge improves not only safety but also speed and efficiency.
Benefits of regular training include:
- Improved turnaround times from faster, more confident equipment use
- Reduced injuries and workers’ compensation claims
- Lower equipment wear due to correct handling
- Fewer costly errors in cargo placement or trailer positioning
Case Study: A facility in Pennsylvania saw a 35% increase in daily shipping volume after implementing a quarterly dock safety training series focused on mechanical levelers, restraint systems, and trailer communication procedures.
Training Topics to Cover:
- Correct use of dock levelers, dock leveler springs, and restraints
- Identifying early signs of worn or broken loading dock parts
- Emergency protocols in the event of equipment failure
- Safe forklift operation on and around the dock
- Proper trailer alignment, parking, and chocking
Tip: Pair hands-on training with visual aids—such as dock signage, floor markings, and LED indicators—to reinforce procedures. Also, include seasonal refreshers to address winter hazards like ice buildup on ramps or seals.
Well-trained personnel are the single most powerful upgrade you can make to your dock efficiency—no capital investment required.
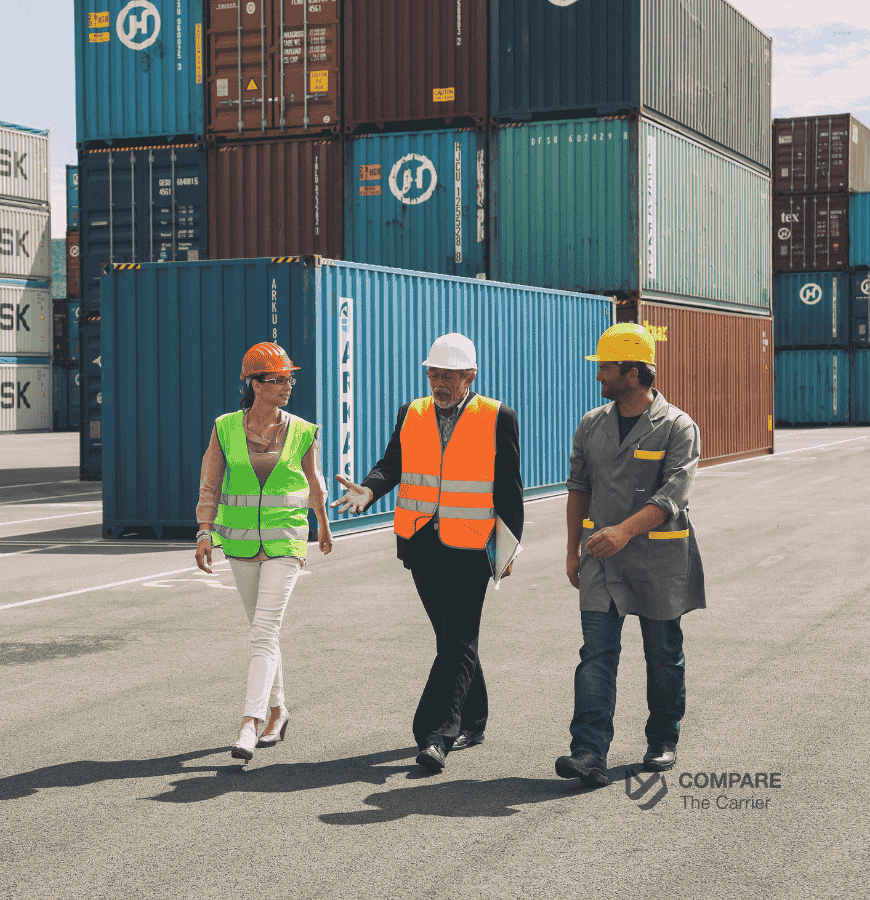
9. Freight Carrier Coordination
Reducing Wait Times & Misalignments
A fully optimized dock can still fall victim to inefficiencies if freight arrivals are poorly timed or miscommunicated. Lack of coordination with freight carriers leads to truck bottlenecks, idle dock workers, missed pickups, and double handling of goods.
According to a 2024 Inbound Logistics report, over 40% of warehouse dwell time is caused by uncoordinated arrivals and poor communication between facility managers and carriers. That’s time your team spends waiting—rather than loading.
Efficient freight carrier coordination ensures:
- Accurate truck arrival scheduling
- Proper trailer types and sizes are matched to available dock bays
- Reduced congestion and dock queueing
- Fewer misaligned trailers, which often result in equipment damage or accidents
Warehouse management systems (WMS) with dock scheduling tools can help automate this process, but even low-tech solutions like shared calendars, real-time updates, and standardized check-in procedures make a difference.
Choosing Carriers Who Understand Docks
Not all freight carriers are created equal—especially when it comes to working with tight loading docks, specialty restraints, or time-sensitive shipments.
Working with professional, experienced carriers helps ensure:
- Drivers are trained in safe and proper trailer docking
- Equipment is compatible with your dock height and vehicle restraints
- Drivers communicate clearly with your loading personnel
A North Carolina distribution center reduced their average dock dwell time by 22% after switching to a regional carrier network that specialized in cross-dock-compatible trucks and assigned experienced drivers who adhered to facility-specific unloading protocols.
Key Insight: Delays caused by unprepared drivers or noncompliant trailers not only slow you down—they put your staff and equipment at risk.
10. Modernisation and Retrofitting
Repair vs. Upgrade
There comes a point when repairing your existing dock infrastructure no longer makes sense—whether due to escalating maintenance costs, outdated safety features, or inefficiency that holds your operations back.
Facilities relying on equipment older than 10–15 years often find that retrofitting or modernizing their loading docks delivers a better return on investment than continually patching old systems. According to Material Handling Industry (MHI) research, companies that modernize dock equipment see an average of 28% improvement in throughput within the first year.
Here’s how to decide between repair and replacement:
- Frequent Breakdowns: Constant part replacements (e.g., dock leveler springs or hydraulic components) signal the system is nearing end-of-life.
- Outdated Safety Compliance: If your current setup doesn’t support vehicle restraints, safety lighting, or OSHA-mandated features, you’re at risk.
- Incompatibility with Modern Trucks: Trailer design has changed—older docks may not align with today’s configurations or sizes.
- High Energy Costs: Legacy docks leak air, especially when paired with degraded seals or inefficient insulation.
ROI of Upgraded Systems
Modernizing your dock doesn’t mean starting from scratch. Retrofitting options allow you to:
- Add hydraulic conversions to manual dock levelers
- Integrate LED dock lighting and motion-sensor systems
- Install energy-efficient dock seals and shelters
- Upgrade to smart vehicle restraints that tie into dock control panels
- Include remote monitoring for predictive maintenance alerts
Example: A Michigan 3PL warehouse retrofitted six manual dock levelers with hydraulic kits and smart locks—resulting in a 31% reduction in turnaround time, fewer worker injuries, and a significant drop in energy consumption from better insulation.
Don’t overlook grants or tax incentives for energy-efficient upgrades either. Many state and local utility programs offer rebates for retrofits that reduce power consumption or improve worker safety.
Tip: Always work with vendors who understand dock equipment parts compatibility, especially when mixing new technologies with older infrastructure. Not all upgrades are plug-and-play.
By thinking proactively about dock modernization, facilities not only solve today’s problems—they position themselves for growth, compliance, and cost control long into the future.
Сonclusion
Optimizing your loading dock isn’t just about better equipment—it’s about building a system where people, parts, and processes work in sync. From upgrading dock leveler springs to training your team and partnering with efficient carriers, each of the ten essentials outlined above plays a role in minimizing risk and maximizing ROI.
For facilities ready to take the next step, using a freight comparison tool like CompareTheCarrier helps connect you with transport companies who understand the value of efficient dock operations—and help keep your workflow moving.
Would you like a downloadable checklist or maintenance calendar to accompany this article?
FAQ
Below are answers to the most common questions we hear from warehouse managers, facility operators, and logistics professionals who deal with dock equipment, maintenance, and shipping coordination—especially when it involves large or specialty cargo like vehicles.
What is a dock leveler and why is it important?
A dock leveler is a platform that bridges the height and gap between a loading dock and a truck trailer. It ensures smooth and safe transfer of goods by adjusting to various trailer heights. Without it, forklifts or pallet jacks would struggle to enter or exit the trailer, risking product damage and injuries.
How do dock leveler springs work?
Dock leveler springs counterbalance the weight of mechanical dock platforms, allowing them to rise and lower with less force. They’re essential for stable operation, especially in manual systems, and should be inspected frequently for wear.
What are the most common parts for loading docks that need replacement?
High-wear items include dock leveler springs, hold-down assemblies, dock bumpers, vehicle restraint parts, dock lights, gaskets, and seals. Keeping spare loading dock parts on hand minimizes downtime when these components fail.
How often should loading dock equipment be inspected?
OSHA and manufacturers recommend monthly visual inspections, with more in-depth quarterly audits. High-traffic facilities may benefit from weekly checklists. This helps prevent accidents and expensive emergency repairs.
How do I know when to replace my dock leveler springs?
Signs include a sagging or unresponsive platform, uneven lifting, creaking noises, or visible rust and stretch in the springs. Replacing them before they snap is safer and far less costly.
What’s the difference between dock seals and shelters?
Seals create a tight compression fit around the trailer and are best for facilities with standard-size trucks. Shelters allow more flexibility with trailer size and movement, using a curtain-style enclosure that creates a weather barrier without contact.
How do I maintain dock lighting for safety and energy efficiency?
Switching to LED dock lights reduces power use and maintenance. Clean fixtures regularly, check lenses for damage, and replace dim bulbs immediately. Proper lighting also supports OSHA’s visibility requirements.
Do I need vehicle restraints if I already use wheel chocks?
Yes. Wheel chocks are manual and prone to human error. Mechanical or hydraulic vehicle restraint systems provide automatic engagement with trailers and integrate safety lighting, significantly reducing the risk of premature departure accidents.
Can I retrofit older dock equipment or do I need full replacements?
Many systems can be upgraded with retrofits like hydraulic kits, safety interlocks, or LED lighting. This approach is more affordable than total replacement and can modernize older docks to meet current efficiency and safety standards.
What are the OSHA requirements for loading docks?
OSHA requires secured trailers, proper lighting, fall protection (guardrails or visual barriers), and regular inspections. Failure to comply can result in heavy fines and legal exposure if injuries occur.
What is “trailer creep” and how can I prevent it?
Trailer creep is the gradual movement of a trailer away from the dock due to repeated forklift entry and exit. It’s prevented by using dock locks or restraint systems that secure the trailer to the dock throughout the loading process.
How can I coordinate shipments better to reduce wait times at the dock?
Use scheduling software or a centralized calendar to plan arrival windows. Choose freight carriers experienced in dock procedures. A platform like CompareTheCarrier helps match you with carriers who understand warehouse dock timing and logistics.
What are dock bumpers, and why are they important?
Dock bumpers absorb the impact when trucks back into the dock, protecting both the building and the trailer. They prevent structural damage, reduce repair costs, and are required by many insurance policies and safety guidelines.
How do I choose the right dock leveler for my facility?
Consider the types of trucks used, average load weight, and available pit size. Options include mechanical, hydraulic, and air-powered levelers. Speak with a dock equipment expert for tailored recommendations based on your volume and dock traffic.
Can loading dock parts be ordered online, and how fast can I get them?
Yes. Many reputable suppliers offer online ordering of parts for loading docks, often with same-day or next-day shipping. Having a supplier with regional warehouses (e.g., in Wisconsin or California) speeds up delivery and reduces downtime.